Mastering Abrasive Blasting: Comprehensive Strategies to Elevate Productivity and Surface Preparation
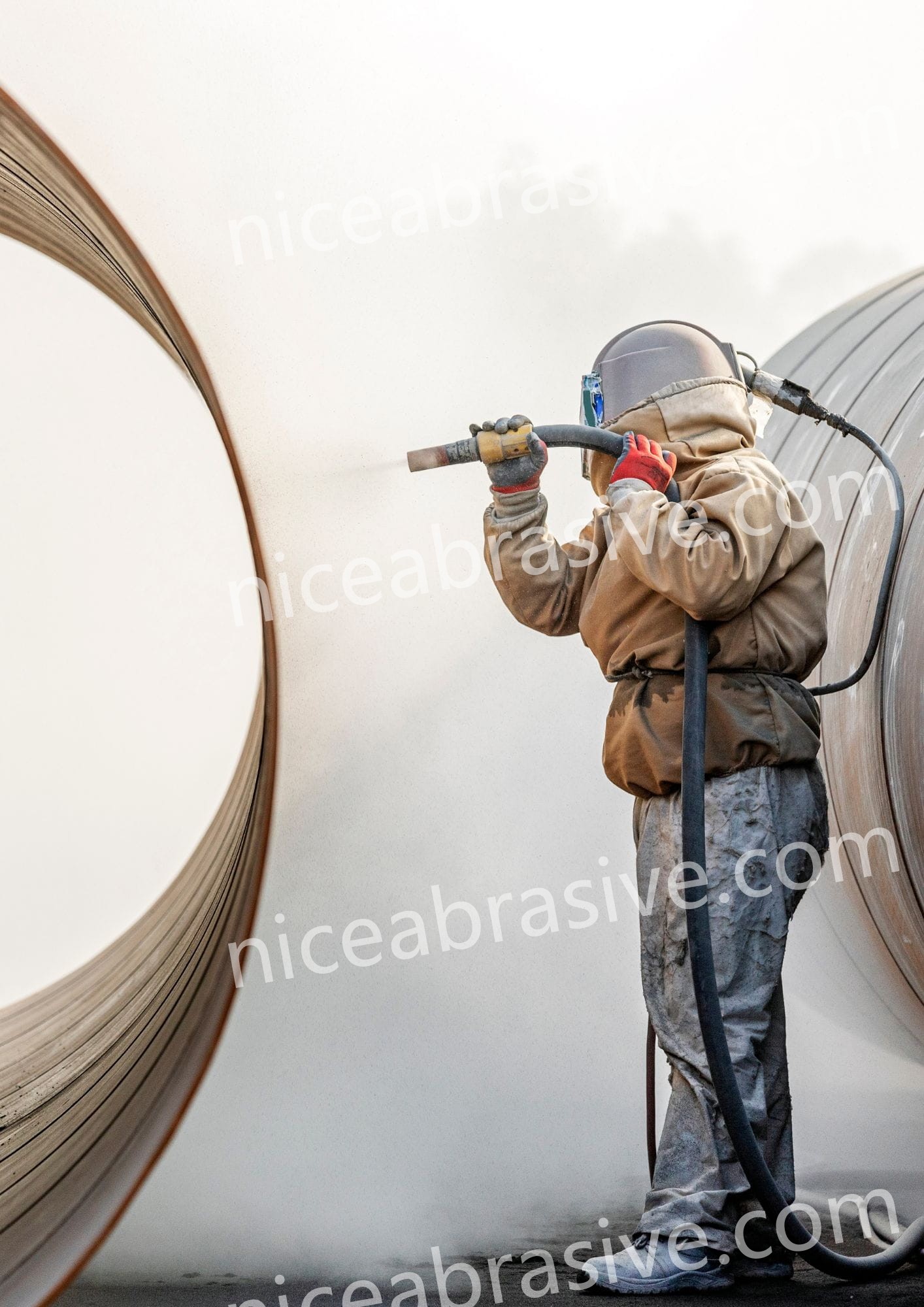
Introduction: The Critical Role of Surface Preparation in Industrial Applications
In the realm of industrial surface preparation, achieving the perfect balance between speed and quality is paramount. Abrasive blasting stands as a cornerstone technique, essential for removing contaminants, rust, and old coatings, thereby ensuring optimal adhesion for subsequent treatments. However, the challenge lies in enhancing productivity without compromising the integrity of the surface. This comprehensive guide delves into advanced strategies, media selection, equipment optimization, and best practices to elevate your abrasive blasting operations.
Understanding the Fundamentals of Abrasive Blasting
What is Abrasive Blasting?
Abrasive blasting, commonly known as sandblasting, involves propelling abrasive materials at high velocities to clean or modify surface properties. This process is instrumental in preparing surfaces for painting, coating, or bonding by creating a suitable profile and removing unwanted substances.
Importance in Surface Preparation
Proper surface preparation is crucial for the longevity and performance of coatings. Inadequate preparation can lead to coating failures, increased maintenance costs, and potential safety hazards. Abrasive blasting ensures surfaces are free from contaminants and possess the desired roughness for optimal coating adhesion.
Selecting the Right Abrasive Media: A Key to Productivity
Choosing the appropriate abrasive media is pivotal in achieving efficient and effective blasting results. Factors such as material hardness, shape, size, and recyclability play significant roles.
Common Types of Abrasive Media
-
Aluminum Oxide: Known for its hardness and sharpness, aluminum oxide is ideal for aggressive cleaning and surface preparation. It is reusable and suitable for a variety of substrates.
-
Glass Beads: These spherical abrasives are perfect for achieving a smooth, bright finish without altering the dimensions of the workpiece. They are reusable and produce minimal dust.
-
Garnet: A natural mineral abrasive, garnet offers high cutting efficiency and is environmentally friendly. It is suitable for both wet and dry blasting applications.
-
Silicon Carbide: As one of the hardest blasting materials, silicon carbide is excellent for removing tough coatings and contaminants. It provides a fine finish and is reusable.
-
Steel Shot and Grit: These metallic abrasives are used for heavy-duty cleaning and surface preparation. They are highly durable and can be recycled multiple times.
-
Plastic Media: Ideal for delicate surfaces, plastic media removes coatings without damaging the substrate. It is commonly used in aerospace and automotive industries.
-
Walnut Shells and Corn Cobs: These biodegradable abrasives are suitable for cleaning soft metals, plastics, and wood without causing damage.
Factors to Consider in Media Selection
-
Hardness: Match the abrasive hardness to the substrate to prevent damage or ineffective cleaning.
-
Shape and Size: Angular particles are more aggressive, while spherical ones are gentler. Particle size affects the surface profile and cleaning rate.
-
Recyclability: Reusable media can reduce costs and environmental impact.
-
Health and Environmental Impact: Choose media that produce minimal dust and are non-toxic to ensure operator safety and environmental compliance.
Enhancing Productivity Through Equipment Optimization
Nozzle Selection and Maintenance
The nozzle is a critical component in the blasting process. Selecting the right nozzle type and size can significantly impact efficiency. Regular inspection and replacement of worn nozzles ensure consistent performance and prevent pressure loss.
Air Pressure and Volume
Maintaining optimal air pressure and volume is essential for effective abrasive propulsion. Ensure compressors are adequately sized and maintained to deliver consistent airflow.
Blast Hose and Fittings
Using appropriately sized and durable hoses minimizes pressure drops and wear. Regular inspection for leaks or damage is necessary to maintain system integrity.
Dust Collection Systems
Implementing efficient dust collection systems enhances visibility, reduces health risks, and complies with environmental regulations. Proper maintenance of these systems ensures their effectiveness.
Implementing Best Practices for Operational Efficiency
Operator Training and Safety
Well-trained operators are crucial for efficient and safe blasting operations. Regular training on equipment handling, safety protocols, and process optimization leads to improved productivity and reduced incidents.
Surface Preparation Standards
Adhering to industry standards, such as those set by the Society for Protective Coatings (SSPC), ensures consistent quality and performance of surface preparation.
Process Monitoring and Quality Control
Implementing monitoring systems to track parameters like pressure, media flow, and surface profile helps in maintaining process consistency and identifying areas for improvement.
Environmental and Health Considerations
Dust and Waste Management
Effective dust suppression and waste management practices are essential to minimize environmental impact and ensure compliance with regulations. Utilizing low-dust media and proper containment systems can significantly reduce airborne contaminants.
Personal Protective Equipment (PPE)
Providing appropriate PPE, including respirators, protective clothing, and eye protection, safeguards operators from potential hazards associated with abrasive blasting.
Conclusion: Achieving Excellence in Abrasive Blasting
Maximizing productivity in abrasive blasting requires a holistic approach that encompasses the selection of suitable media, equipment optimization, adherence to best practices, and consideration of environmental and health factors. By implementing these strategies, industries can enhance surface preparation quality, reduce operational costs, and ensure the longevity of protective coatings.