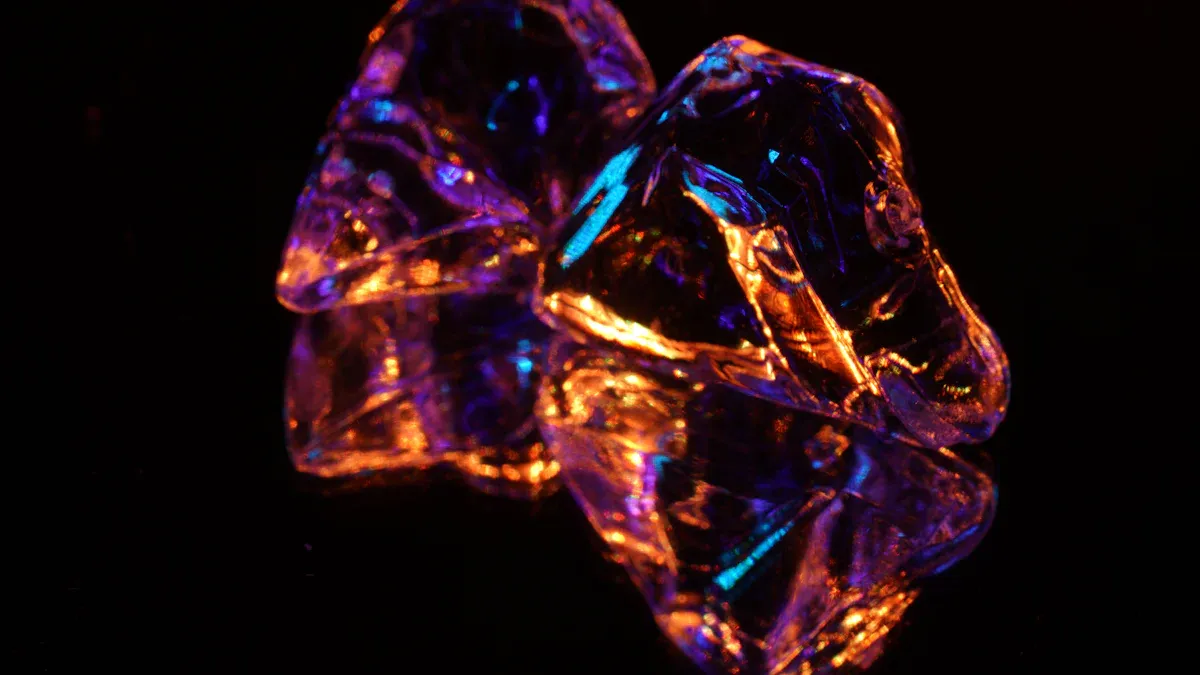
Black silicon carbide is a man-made ceramic made from silicon and carbon. This material is very hard, tough, and can break easily. It does not get damaged by heat or rust, so it works well in tough places. Black silicon carbide has more than 95% SiC, so it is stronger than many other materials. Its hardness is between corundum and diamond. This makes it good for grinding cast iron, glass, ceramics, and stone. Many industries use it because it stays stable with chemicals, moves heat well, and does not wear out fast.
Key Takeaways
- Black silicon carbide is very hard and strong. It is made mostly from silicon and carbon. People use it to grind, cut, and polish hard things.
- It does not break down from heat, chemicals, or wear. It stays strong even when it gets as hot as 1600°C. This makes it good for tough factory work.
- Black silicon carbide is not as pure or hard as green silicon carbide. But it is tougher and better for most factory jobs.
- Its sharp grains and heat resistance help tools last longer. Tools also work faster, which saves time and money for many businesses.
- Black silicon carbide is used in many ways. It is in abrasives, bricks that resist heat, metal work, glass shaping, electronics, and water filters because of its special features.
Black Silicon Carbide
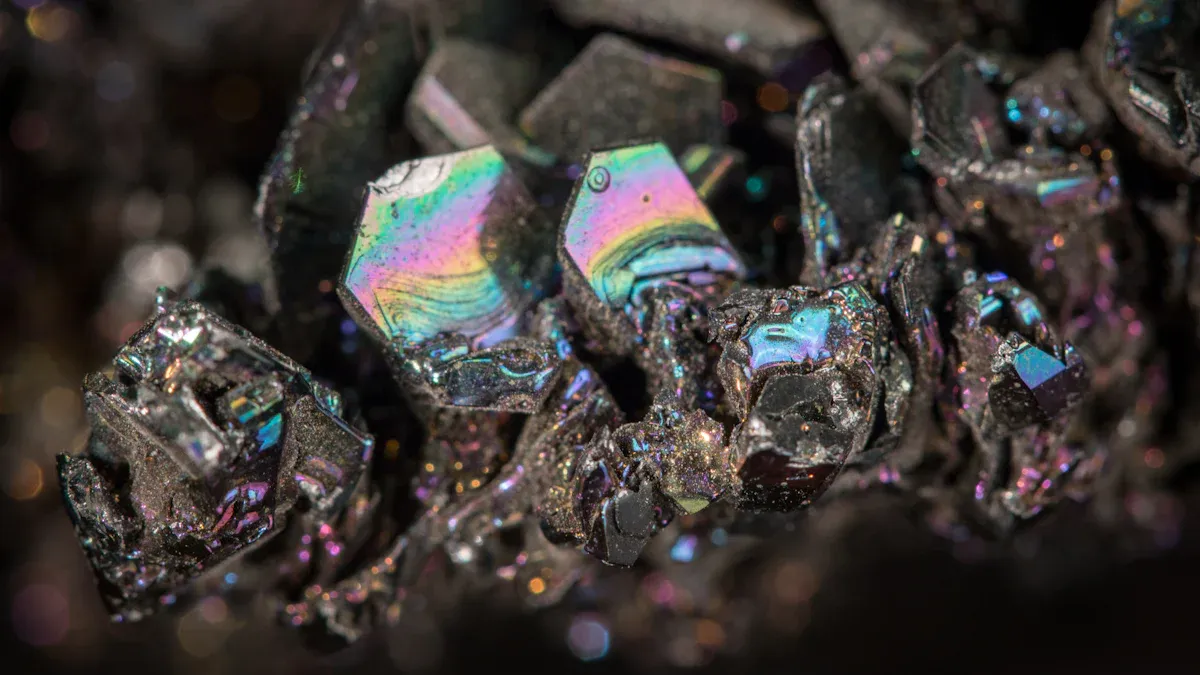
Definition
Black silicon carbide is made by mixing silicon and carbon. This happens at very high heat. Scientists look at its chemical makeup, how it is made, color, and physical traits. The table below shows the main ways to tell what black silicon carbide is:
Aspect | Description |
---|---|
Chemical Composition | It is mostly silicon carbide with a little iron and carbon. These make it look black. |
Production Method | It is made by heating sand and petroleum coke in a special furnace at about 2500°C. |
Color | The color is black because of leftover impurities from making it. |
Physical Properties | It is very hard, lets heat move through it well, does not break easily with heat, and does not expand much. |
Particle Characteristics | How big the pieces are, how pure it is, and how the grains are spread out change how it works and where it can be used. |
Composition
Black silicon carbide has almost equal amounts of silicon and carbon. It is about 95% silicon carbide. The rest is small amounts of other things. Carbon black makes up 9% to 18% of it. When carbon black is between 12% and 15%, it is the strongest. Its density is between 2.70 and 2.85 grams per cubic centimeter. Porosity is between 3.99% and 0.39%. These numbers show how makers change the mix to get the best results.
- Carbon black: 9–18 vol%
- Best strength: 12–15 vol% carbon black
- Density: 2.70–2.85 g/cm³
- Porosity: 3.99–0.39 vol%
Silicon Carbide Type | SiC Content (%) | Approximate Si:C Atomic Ratio |
---|---|---|
Black Silicon Carbide | ~95% | ~1:1 (almost equal) |
Green Silicon Carbide | ~97% | ~1:1 (almost equal) |
Production
Black silicon carbide is made using the Acheson process. Makers heat sand and petroleum coke in a furnace at about 2500°C. This forms silicon carbide crystals. The crystals are then broken up and sorted by size. How good the product is depends on things like the optical texture index of the coke and how much nickel and iron are in it. More nickel and iron help make more silicon carbide. Vanadium does not help as much. Coke with low vanadium and a good structure is best for making it in factories.
The chart below shows how the optical texture index, nickel, and temperature change the amount and quality of black silicon carbide made:
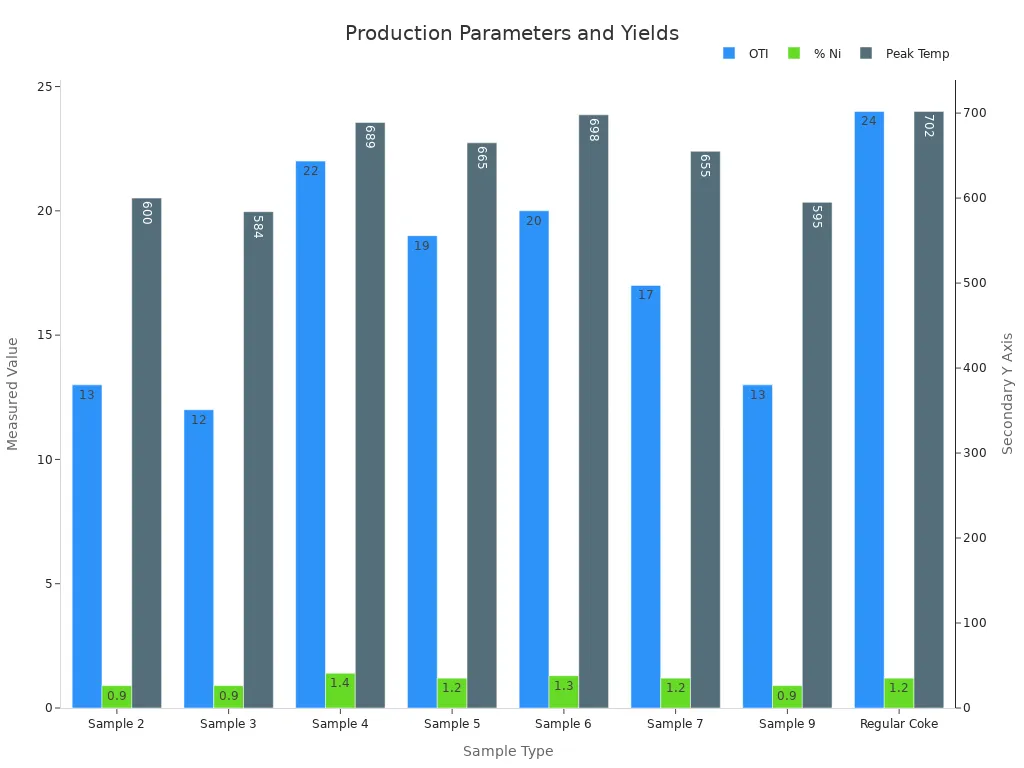
Note: You can guess how much is made with this formula:
yield (%) = 8 × (OTI)^0.5 + 36 × (%Ni) + 34 × (%Fe) + 3 × (%V).
This helps makers get better at making black silicon carbide.
Properties
Physical
Black silicon carbide has some very strong physical features. Its Mohs hardness is 9.5, which is almost as hard as diamond. This makes it one of the hardest materials used in factories. On another hardness scale, it gets a score of 13. Because it is so hard, it can cut, grind, and polish things like glass, ceramics, and stone.
- Mohs hardness: 9.5
- It is tough but can break easily
- It looks dark black because of leftover carbon and other stuff
Property | Value |
---|---|
Mohs Hardness | 13 (new scale) |
Specific Density | 3.21 g/cm³ |
Black silicon carbide has a density of about 3.21 grams per cubic centimeter. Its grains are sharp and have corners, which helps it cut better. It is tough, so it does not crack easily under pressure. But it can break if hit hard. These features make black silicon carbide a good choice for jobs that need strong abrasives.
Chemical
Black silicon carbide is very stable with chemicals. A thin layer of silica forms on its surface by itself. This layer protects it from rust and damage. The silica slows down reactions with air and other things, so the material lasts longer in harsh places. It does not rust easily, but some gases like hydrogen and water vapor at high heat can damage the protective layer. This can cause more rust.
Tests show the silica layer also helps stop wear by acting like a slippery cover when things slide against it. If you take off this layer, the material wears out faster. Special tests, like X-ray diffraction and electron microscopes, show there are carbon black particles inside the silicon carbide. These particles help keep the material strong, even in tough situations. When tested at 300 °C, black silicon carbide keeps its shape and does not change, so it works well in nuclear and other hard jobs.
Mechanical & Thermal
Black silicon carbide is strong and handles heat very well. Its strong bonds make it hard, tough, and able to resist wearing out. Tests on materials mixed with silicon carbide show they get stronger and last longer. Black silicon carbide keeps its strength up to 1600 °C, so it is great for hot places.
It moves heat quickly, so it does not get too hot in one spot. It does not get bigger or smaller much when the temperature changes. This means it does not crack or break easily when heated or cooled fast. These features are better than what many factories need for abrasives, heat-resistant bricks, and heat control.
- Moves heat well
- Does not expand much with heat
- Stays strong after many heating and cooling cycles
- Keeps its strength even when very hot
Tests show black silicon carbide does not break after being heated and cooled many times. Even after 100 cycles, it does not change in weight, color, or density. Because of these features, it works well in places with lots of heat and stress.
Comparison
Black vs. Green
Black silicon carbide and green silicon carbide are a lot alike. But they also have some big differences. Black silicon carbide is made without industrial salt. This way of making it leaves some carbon inside. The carbon makes it look black and a little less hard. Black silicon carbide has a Mohs hardness of about 9.1. People use it to grind cast iron and soft metals. It is also used for sandblasting and making heat-resistant products.
Green silicon carbide is made with industrial salt. This makes it much purer, about 99% pure. Small amounts of chromium or titanium give it a green color. Green silicon carbide is harder, with a Mohs hardness of about 9.4. It can handle shocks better and moves heat faster. It also does not react with chemicals as much. These things make it good for grinding hard and brittle things like carbides and ceramics. Many companies use green silicon carbide for making lenses and computer chips.
Note: You should pick black or green silicon carbide based on the job. Green silicon carbide is best for very careful work. Black silicon carbide is used more for regular factory jobs.
Key Differences
The table below shows the main ways black and green silicon carbide are not the same:
Property | Green Silicon Carbide | Black Silicon Carbide |
---|---|---|
Purity | ~99% | 97-99% |
Mohs Hardness | ~9.4 | ~9.1 |
Knoop Hardness | 2840 | 2680 |
Relative Toughness | 1.6 | 1.75 |
Morphology | Sharp, angular, glassy | Sharp, angular, glassy |
Typical Applications | Grinding carbides, ceramics, optical and semiconductor industries | Grinding cast iron, ductile non-ferrous metals, sandblasting, refractory uses |
Chemical Composition | Contains trace elements like chromium or titanium (green hue) | Contains carbon impurities (black color) |
Other Properties | Better shock resistance, thermal conductivity, chemical stability, corrosion resistance | Slightly less hard but tougher |
Green silicon carbide is more pure and harder than black silicon carbide. It can handle chemicals and heat better. Black silicon carbide is tougher, so it does not break as easily. Each type is used for different jobs because of these differences.
Uses of Black Silicon Carbide
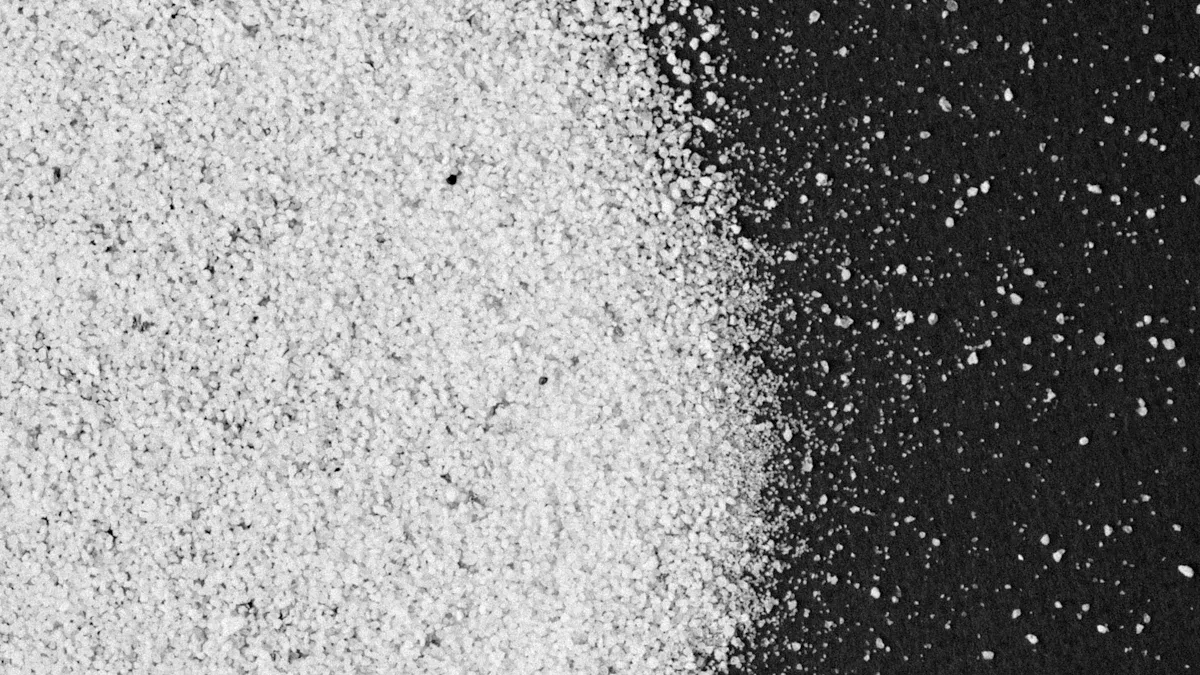
Abrasives
Many factories use Black Silicon Carbide for making abrasive tools. It is very hard and has sharp grains. This makes it great for grinding, cutting, and polishing tough things. People put it in sandpaper and grinding wheels. It is also in lapping compounds. The material takes off metal and stone fast because it stays sharp. When the grains break, they make new sharp edges. This means the tools keep working well for a long time.
The table below shows how Black Silicon Carbide and aluminum oxide compare in abrasive jobs:
Metric | Black Silicon Carbide (SiC) | Aluminum Oxide (Al₂O₃) |
---|---|---|
Material Removal Rate (MRR) | 28% faster | Baseline |
Belt Life | ~35% longer | Baseline |
Surface Finish (Ra) | 0.20–0.30 µm | 0.35–0.50 µm |
Grinding Energy Consumption | 16.5 J/mm³ | 22.0 J/mm³ |
Wear Resistance (G-ratio) | 10–12 | 6–8 |
Burn Risk | Low | Moderate |
Black Silicon Carbide can handle heat very well. It moves heat away fast during grinding. This keeps the tool and the thing being worked on safe. It lowers the chance of burns and keeps the surface smooth.
Refractories & Metallurgy
Factories use Black Silicon Carbide to make things that can take a lot of heat. It is used for bricks, kiln furniture, and furnace linings. The material does not get damaged by heat or chemicals. It also does not break when the temperature changes fast. These things help it last longer in tough places. In metallurgy, workers add it to melted metals. This makes the metal stronger and helps clean out bad stuff. It does not react with the metal, so the process stays clean.
Other Applications
Black Silicon Carbide is used in many other ways. Glass makers use it to shape and etch glass. Electronics companies use it as a base for semiconductors. It can handle high voltage and heat. Some people use it in water filters and advanced ceramics. Its mix of hardness, toughness, and chemical resistance makes it a good pick for hard jobs.
Tip: If you need to grind, cut, or work with heat, think about using Black Silicon Carbide. It works well, lasts long, and can handle tough jobs.
Black Silicon Carbide is very hard and has sharp edges. It does not get damaged by most chemicals. These things make it great for grinding and cutting. It is also good for polishing and lining furnaces. Black Silicon Carbide works well in tough places. It stays strong when it gets hot or touches chemicals. Many factories use it because it lasts long and saves money. Engineers should think about using it for hard jobs because of these special features.
FAQ
What makes black silicon carbide different from other abrasives?
Black silicon carbide is very hard and has sharp grains. It can cut and grind things faster than most other abrasives. Factories use it for tough jobs because it lasts longer. It also works well when things get hot.
Can black silicon carbide handle extreme temperatures?
Yes, it can. Black silicon carbide stays strong up to 1600 °C. It does not crack or change shape after being heated and cooled many times. This makes it good for furnaces and other hot places.
Is black silicon carbide safe for use with food or water?
Black silicon carbide does not react with most chemicals. Some water filters use it. But makers must check if it is safe before using it with food or water.
How does black silicon carbide compare to green silicon carbide?
Feature | Black SiC | Green SiC |
---|---|---|
Hardness | A bit lower | Higher |
Purity | Lower | Higher |
Typical Use | General industry | Precision tasks |
Green silicon carbide is more pure and harder. Black silicon carbide is tougher and used more in factories.